As a large-scale mechatronics equipment, automotive electronics is becoming more and more important in the overall cost of automobiles. At present, the average cost of automotive electronics in developed countries in Europe and America is more than 350 US dollars, covering everything from body control, power transmission, body safety to in-car entertainment.
This article refers to the address: http://
Microcontrollers (MCUs) are the core of the internal processing and processing of automotive electronic systems, and are also used in dozens of sub-systems such as suspension, airbags, gating and sound. Since the car as a high-speed vehicle carries the safety guarantee for the user's life, and the car often works in a very harsh environment, the reliability requirement for the internal electronic device is much higher than that of the general electronic product. Therefore, the structural difference between the MCU used in automotive electronics and the general product is not very large, and the general MCU product cannot be selected because the reliability cannot meet the requirements of the manufacturer. This is also the market for automotive electronics and the general electronic product market. One of the differences.
Technical characteristics
CAN and LIN are the most common body system bus interfaces. Therefore, in addition to high reliability and resistance to harsh environments, automotive electronic MCUs must also support the above bus interfaces.
The CAN bus is the Controller Area Net. It is a field bus. It was originally designed by German BOSCH for vehicle monitoring and control. It is mainly used for various process detection and control. The CAN bus is divided into high-speed CAN and low-speed CAN. The former is mainly used for critical applications such as power and safety, such as engine control unit, automatic transmission control, ABS control, airbag control, etc.; the latter is usually for general body applications. Such as centralized locks, luggage locks, windows, and interior lighting. The CAN bus protocol is also evolving. From the earliest 1.x version to the current CAN2.0A and its extended version of CAN2.0B, CAN2.0B is divided into active (active) and passive (Passive). )formula.
Due to the different versions and classifications of the CAN bus protocol, there are also differences in the requirements for automotive MCUs. In addition to the protocol versions mentioned, the number of CAN bus controller buffers and receive filters also affects the choice of MCU. As shown in the figure, ST's CAN controller has five different types of pCAN, beCAN, bxCAN, FullCAN and cCAN for different application scenarios. Among them, beCAN and bxCAN are suitable for mid-to-high-end body function control and low-end gateway; FullCAN is suitable for engine management system; cCAN is suitable for high-end gateway and power transmission control.
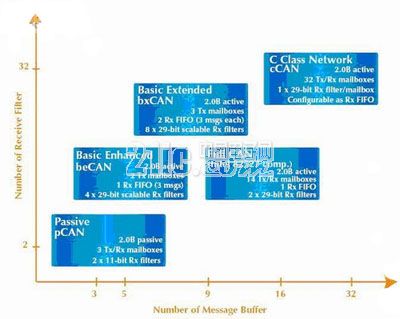
Figure 1 Number of buffers and receive filters for different CAN controllers
The LIN (Local Interconnect Network) bus is a new low-speed serial bus with simple structure, flexible configuration and low cost. It is mainly used as an auxiliary network or sub-network of high-speed bus such as CAN. In areas where bandwidth requirements are low, functions are simple, and real-time requirements are low, such as control of body appliances, the use of LIN bus can effectively simplify network wiring harnesses, reduce costs, and improve network communication efficiency and reliability. As shown, LIN is mainly suitable for Air-Conditioning Control, Door Modules, Seat Control, Smart Switches, Low-Cost Sensors. Such as distributed communication applications.
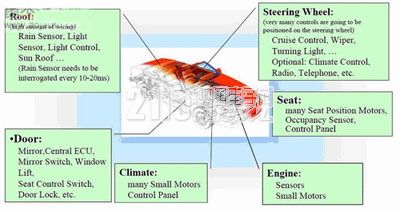
Figure 2 LIN application area
Gateway controller
The gateway function of the in-vehicle gateway (Gateway) is the communication hub of different networks in the in-vehicle electronic system, so that the units distributed in the vehicle body can communicate. Gateways typically include bus transceivers, Regulators, and low-cost, high-performance microcontrollers that support multiple network protocols; and support for low-speed and high-speed automotive communications such as CAN, LIN, ISO-9141, and J1850 interface. The gateway controller is designed to be flexible, and the general manufacturer will customize it according to its own needs. For different applications, it can be integrated into devices such as body control units or instrument clusters, or it can be used as a stand-alone module.
The role of embedded flash
The embedded memory of the MCU can guarantee the requirements of the industrial computer system, the stability can be improved, and the lower cost and the flexibility of the work processing can be realized. Therefore, providing embedded memory on the MCU, and even integrating the DSP unit, has become the current design trend.
The embedded memory of the vehicle MCU includes ROM, EEPROM, RAM and Flash. Among them, the memory of the microcontroller program and the data storage of the NOR Flash can make the MCU have higher flexibility, and has gradually become the mainstream of the current design. Since the MCU does not need to be connected in series with external components due to the embedded memory, it is not easy to cause signal interference, which reduces the complexity of the wiring and improves the stability. In addition, the embedded memory eliminates the need for external components, and can also effectively reduce the PCB size and give the product greater flexibility. In terms of data security, the data protection mechanism of the MCU embedded memory can achieve high reliability and ensure that the data is protected from theft.
DSP enhances design flexibility
Digital signal processing (DSP) technology is the technical foundation of today's high-tech digital industry. From the MP3 to hear high-tech applications such as aerospace, DSP technology is ubiquitous and growing rapidly. In the design of automotive electronic systems, in addition to the above mentioned embedded memory in the MCU, adding the MAC function of the DSP to the MCU can also effectively improve the flexibility of data processing. DSP is a software functional area of ​​the system, so it can flexibly perform functional improvements and upgrades according to the needs of the manufacturer or customer. In addition, DSP and processor (ARM, PowerPC, etc.) can be combined to achieve multi-task division processing, for example, the key control functions can be completed by the processor, and DSP can be dedicated to the operation of the operation, which can reduce system power consumption. And improve processing efficiency.
DSPs are typically used to process large numbers of digital signals, codecs, and communication data analysis. In automotive electronic systems, such as on-board auxiliary road condition warning safety systems, the DSP can be used to process and identify complex road condition information and provide real-time advice and warnings to drivers in a timely manner.
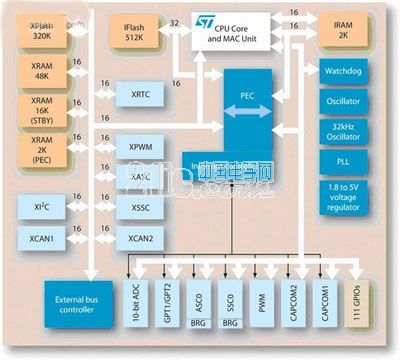
Figure 3: 16-bit MCU with MAC unit (take ST10 as an example)
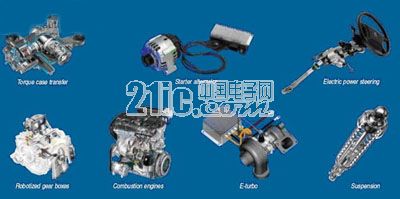
Figure 4 Application scenario of 16-bit vehicle MCU
MCU processing power and application
The market for in-vehicle MCUs is mainly focused on the 8, 16 and 32-bit microcontrollers, which can be used for different performance scenarios according to the different needs of automotive electronics.
8-bit MCUs are mainly used in relatively simple systems such as fans, air conditioners, wipers, windows, junction boxes, seat controls, and door controls due to processing power limitations. The 16-bit MCU is generally used in mid-range equipment. The main applications are engine control, clutch control, chassis mechanism and suspension, electronic brakes, electronic power steering, and electronic turbine systems. The 32-bit MCU is mainly used in the automotive electronics field for pre-crash modules, adaptive cruise control (ACC), driver assistance systems, electronic stability programs and other safety functions, and complex X-by-wire transmission functions. Modules that require high intelligence, computing performance, and real-time performance, such as telematics, security systems, and engine control.
Currently, the living space of 16-bit MCUs seems to be continually squeezed by 8-bit and 32-bit MCUs. 8-bit microcontrollers continue to increase the power of the processor core, with the increase in embedded memory capacity and the more flexible number of pins, coupled with mature technology to further reduce costs, making the 8-bit microcontroller suitable for the market The space is getting bigger and can cover up to some 16-bit MCU applications, and can also replace most 4-bit MCUs down. 32-bit MCUs have a market potential with increasing emphasis on intelligence, real-time and diversity. In addition to handling complex computing and control functions, 32-bit MCU products will also play the role of master processing center in automotive electronic systems. That is, centralized management of low- and medium-level electronic control units (ECUs) scattered throughout. These capabilities are not available to 16-bit MCUs.
The 16-bit MCU seems to be in a very embarrassing situation, but with the addition of higher-capacity memory and the DSP-MAC mentioned above, 16-bit products can still meet the needs of special application functions. Moreover, it has gained market acceptance in terms of component quality, performance, and cost, and there is still an appropriate market space. On the other hand, although 32-bit MCU products have been widely used in the general market, they are currently found in high-end automotive products. In most critical applications such as transmission and safety systems, 16-bit MCUs are still the mainstay. The main reason is that most of the 32-bit MCUs are still in the verification stage of automotive electronic parts specifications, and then need to pass various environmental tests of the vehicle manufacturers themselves, so it will take a while to become the mainstream of the market.
8-bit MCU
As mentioned above, 8-bit automotive MCUs typically require systems to provide fast execution speed and data processing capabilities, efficient Context Switching and memory usage, flexible I/O, and extensive system functionality extensibility. In addition, it also requires support for CAN and LIN bus protocol interfaces, and will be embedded in Flash or ROM, suitable for a wide range of low-end system applications. ST72561 is an 8-bit MCU designed by ST for the automotive environment. It integrates CAN and LIN bus interfaces, has powerful error diagnosis and signal processing functions, low standby power consumption, less than 50μA, and periodic wake-up function. The ST72561 supports the BeCAN control unit based on the Bosch CAN core with a new processor interface. It integrates two transfer mailboxes, three RX-FIFOs, and six filter groups to efficiently filter information by ID. In addition, Its CAN controller fully supports a 29-bit identification code with enhanced message filtering. The LIN interface of ST72561 is oriented to ST's optimization technology such as "master-slave LINSCI connection interface" proposed for hardware design, which can automatically perform header processing and filtering on LIN bus data. This mechanism can greatly reduce the system burden and cost, simplify the circuit design, and greatly improve the system performance. According to tests, up to 90% of the CPU load for LIN bus communication can be saved.
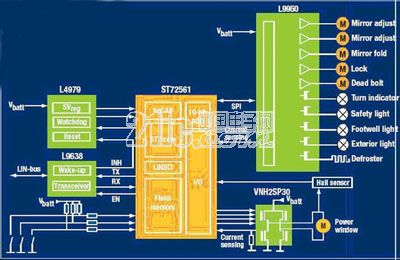
Figure 5 ST7261 system architecture on the car body application
2. 16-bit MCU
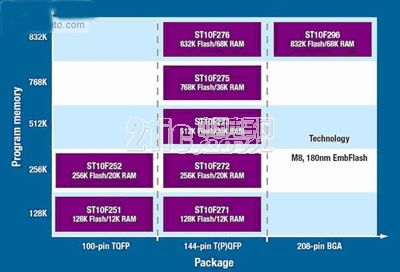
Figure 6: Selection and classification of 16-bit car MCU by memory and package pin number
ST's ST10 is a 16-bit automotive MCU that is suitable for high-performance, high-real-time, and low-power applications such as body drive, chassis and safety systems. The family offers 16 priority interrupt controllers and tightly integrated DMA with CPU frequencies up to 64MHz, making them ideal for demanding hard real-time applications.
The ST10 has a DSP-MAC function. Its DSP-MAC multiply/accumulate accelerator provides powerful DSP functions and a complete library of math software to make self-defined algorithms faster and easier. ST10 has built-in high-capacity flash memory with a capacity of up to 832KB, which can achieve more than 100,000 erase and write times. The ST10 is highly compatible and supports a wide range of system peripherals and interfaces such as ASC/LIN, CAN, I2C and SSC. ST10's cross-platform development capabilities provide potential protection for users' upfront investment. In addition to supporting ST's development tools, it also supports Infineon's C16x and XC16x platforms, providing a quick way for existing users to upgrade to higher density flash. In addition, thanks to ST's latest 0.18μm manufacturing process, and a large operating temperature range (-40 ° C ~ +125 ° C), the product life is effectively extended, data retention time can be up to 20 years. Helps extend product life and optimize costs.
3. 32-bit MCU
32-bit automotive MCUs have higher processing power and higher troubleshooting capabilities than 8-bit and 16-bit MCUs, but for various reasons, their popularity will take some time.
There are many factors affecting the competitiveness of 32-bit MCUs at present, and the cost issue is one of them. Single-chip is an inevitable trend of low cost. If some peripheral circuits such as bus switches, interrupt controllers and troubleshooting circuits are integrated into the MCU, the cost can be effectively reduced. In addition, the single-chip solution can also reduce the size of the product and promote small size. The high frequency circuit interference can also be reduced. On the other hand, low-cost implementations require more optimized and cost-effective production processes and processing technologies to support.
Given the superior processing power of 32-bit MCUs, the most widely used applications today are high-end multimedia devices for automobiles. 32-bit MCUs can further improve the real-time performance of the overall system communication if it is equipped with a higher-speed bus interface such as FlexRay.
The STA2058 is a 32-bit automotive MCU product from ST. Its excellent performance and flexible architecture make it ideal for automotive multimedia information systems (Telematics). STA2058 integrates 32-bit ARM7TDMI microprocessor and embedded flash (Embedded Flash), widely supports CAN, SPI, UART, I2C, USB and other interfaces, as well as RTCA-SC159, WAAS, EGNOS and other GPS systems. In addition, STA2058EX has an external memory interface, which can be used as a telematics service platform, allowing connection to external devices such as GSM/GPRS module, chip card, and audio function DSP through glueless logic (Glueless).
in conclusion
The proportion of automotive electronics in overall vehicle cost is becoming more and more significant, and the importance of MCU is constantly improving. Automotive electronics has its own special thresholds, namely safety and reliability considerations. Therefore, while achieving high intelligence, maneuverability, real-time, and flexibility, the MCU must meet the high standard reliability requirements to ensure safe driving.
Smd Led,Smd Fnd Display,Smd Led 0603 Display,Smd Led 0805 Display
Wuxi Ark Technology Electronic Co.,Ltd. , https://www.arkledcn.com