1 Introduction
Fuel cell vehicles are a type of electric vehicles. The electricity generated by the fuel cell supplies power to the motor through inverters, controllers, and other devices, and then drives the wheels to rotate through the transmission system, drive axle, etc., so that the vehicle can be driven on the road. 2-3 times. The fuel cell chemical reaction process will not produce harmful products, so the fuel cell vehicle is a pollution-free vehicle [1-3]. With the requirements for automobile fuel economy and environmental protection, the automotive power system will gradually transition from now mainly fossil fuels such as gasoline to hybrid power, and will eventually be completely replaced by clean fuel cell vehicles [4].
In recent years, fuel cell system and fuel cell vehicle technology have made significant progress [4-5]. World-renowned automobile manufacturers such as Toyota, Honda, General Motors, DaimlerChrysler, Nissan and Ford Motor Company have developed several generations of fuel cell vehicles [5-12], and announced a variety of fuel cell vehicles to market strategy
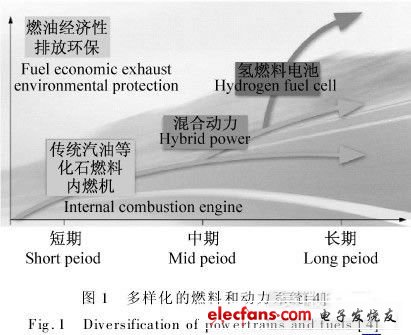
aims. At present, prototype vehicles of fuel cell cars are being tested, and transportation buses powered by fuel cells are undergoing demonstration projects in several cities in North America. Among them, Honda's FCX Clarity has reached a maximum speed of 160 km / h [8]; Toyota's FCHV-adv has run a cumulative 360,000 km road test, can start at minus 37 degrees, and can drive from Osaka to Tokyo in one hydrogen refueling (560 kilometers) [7]. With the support of China's Ministry of Science and Technology, fuel cell vehicle technology has developed rapidly. In 2007, China's fourth-generation fuel cell car was successfully developed, with a maximum speed of 150 km / h and a maximum driving range of 319 km. In 2008, 20 fuel cell demonstration vehicles were again demonstrated at the Beijing Olympics. In 2010, a total of 196 fuel cell vehicles, including domestic automobile companies such as SAIC and Chery, conducted demonstration operations in the Shanghai World Expo Park [13].
There are still technical challenges in the development of fuel cell vehicles, such as the integration of fuel cell stacks, improved commercialization of electric vehicle fuel processors, and auxiliary car manufacturers are all striving to integrate components and reduce component costs. Significant progress has been made. But compared with traditional internal combustion engine cars, fuel cell electric vehicles use "fuel cell + electric motor" to replace the "heart" of the traditional car-engine and fuel system. The fuel cell car's power transmission system has undergone major changes, mainly manifested in: the electric motor replaces the internal combustion engine as the driving power source; the clutch and the torsional shock absorber are omitted; the multi-speed transmission is usually replaced with a reducer [14,15]. Therefore, the power transmission system of fuel cell vehicles is simplified overall. However, when driving, the fuel cell is the main source of power, and the battery is the auxiliary energy source. The power required by automobiles is mainly provided by fuel cells. It can be said that the selection of fuel cells for vehicles is crucial to the performance of fuel cell vehicles.
This paper introduces the development of traditional fuel cell vehicle power technology, and discusses in detail the key technologies such as fuel cell electric vehicle power transmission topology, multi-source system management, power system configuration and simulation optimization technology.
2 Topology design of power transmission system
The operation of a fuel cell vehicle is not a steady state. Frequent start-ups, accelerations, and hill climbs make the vehicle's dynamic operating conditions very complicated. The dynamic response of the fuel cell system is relatively slow, and the output characteristics of the fuel cell cannot meet the driving requirements of the vehicle during startup, rapid acceleration, or climbing steep slopes. In actual fuel cell vehicles, it is often necessary to use a fuel cell hybrid electric vehicle design method, that is, the introduction of auxiliary energy devices (battery, super capacitor or battery ten super capacitor) through the power electronic device and the fuel cell grid, to provide peak power to To supplement the lack of fuel cell power output capacity when the vehicle is accelerating or climbing. On the other hand, under idling, low-speed or deceleration conditions, when the power of the fuel cell is greater than the driving power, the surplus energy is stored, or during the feedback braking, the stored braking energy is absorbed, thereby increasing the energy of the entire power system effectiveness.
2.1 Structure of direct fuel cell hybrid power system
The power electronic device used in the direct fuel cell hybrid power system structure only has a motor controller, and the fuel cell and the auxiliary power device are directly connected in parallel to the entrance of the motor controller. Such as Toyota FCHV-4 [16], FIAT-Elettra [17] and Nissan X-TrailFCV [12], etc. have adopted this similar structural design.
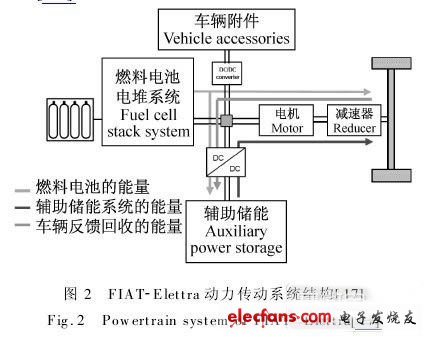
The auxiliary power device expands the total energy capacity of the power system and increases the driving range of the vehicle after one hydrogenation; it expands the power range of the system and reduces the power load borne by the fuel cell. Many plug-in hybrid fuel cell vehicles also often adopt such a framework, the United States Ford's Edge Plug-in fuel cell car and GM's Volt Plug-in fuel cell car [18]. This plug-in hybrid electric vehicle will effectively reduce the consumption of hydrogen fuel. In addition, the existence of the auxiliary power device makes the system capable of recovering braking energy, and increases the reliability of the system operation. The reasonable distribution of load power between the fuel cell and the auxiliary power unit can also improve the overall operating efficiency of the fuel cell [4].
In the system design, a bidirectional DC / DC converter can be added between the auxiliary power unit and the power system DC bus. It makes the control of the charge and discharge of the auxiliary power device more flexible and easy to implement. Since the bidirectional DC / DC converter can better control the voltage or current of the auxiliary power unit, it is also an execution component of the system control strategy.
power adapter from the power transformer, rectifier circuit, shell composition. 9V Power Adapter is a small power adapter, DC cable connector diameter (d) is 2.1mm, diameter (D) is 5.5mm, thickness (B) is 10mm. 5V Power Adapter is high-speed operation and durable, not easy to bad. These power adapter features: product size: 74 * 30 * 42mm, small size, streamlined, completely sealed, easy to carry.cost-effective, high reliability, ultrasonic pressure shell. built-in over voltage, overcurrent and short circuit protection. Products with strong anti-interference, to ensure the use of long life products, through the EMC test, ripple ≤ 50MV.Widely used in Monitor,router and other products.Output conventional voltage 5V 12V 24V 36V 48V, the other can be produced according to customer requirements.
9V AC DC Switching Power Adapter
9 Volt Dc Power Adapter,9 Volt Power Adapter,9 Volt Ac Adapter,9V Ac Power Adapter
Shenzhen Juyuanhai Electronic Co., Ltd. , https://www.powersupplycn.com